Cavity Barriers: Definition, Regulations, and Design
Definition:
A cavity barrier or cavity barriers , are defined by Approved Document B Volume 2, is a construction element designed to seal concealed spaces and prevent the penetration or spread of smoke or flame. Building Regulations specify integrity and insulation performance requirements, with England, Wales, and Northern Ireland requiring 30 minutes’ integrity and 15 minutes’ insulation, while insulation is not mandatory in Scotland.
Regulations:
Building Regulations stipulate that cavity barriers must meet performance standards through testing or assessment. Fire engineered and insurance-driven specifications often require an EI30 performance classification, indicating 30 minutes of integrity and insulation.
Positioning and Design:
According to AD B, cavity barriers in rainscreen walls should be placed at junctions with compartment walls or floors, around window openings, and to limit cavity dimensions. NHBC design guides recommend horizontal barriers at each floor level, vertical barriers at centers no more than 6m apart, and vertical cavity closers within 1.5m of corners. Ventilation and drainage requirements in ventilated facades pose challenges, which are addressed by using intumescent materials that maintain the desired air gap but expand to seal the cavity in case of fire.
Functional Requirements:
Cavity barriers must balance the need for ventilation and fire sealing. Intumescent materials activate around 130°C, expanding to close the void and restore integrity. Manufacturers consider the CWCT standard for guidance on required air gap sizes, which vary depending on joint types in rainscreens.
Cavity barriers are construction elements that seal concealed spaces against smoke and flame. They must meet integrity and insulation requirements set by Building Regulations. Proper positioning and design considerations ensure effective performance in controlling fire spread. Intumescent materials address the challenge of ventilation and fire sealing. Compliance with standards and guidelines contributes to the safety and performance of cavity barriers in building facades.

When considering the reduced gap at fire barriers, this equates to a minimum 12.5mm for sealed and closed joints, a 19mm minimum gap for labyrinth and baffled joints and a 25mm minimum gap for open joints.
As regards testing, different scale fire tests are used for different applications. They range from small-scale to large. Small-scale tests on linear joint seals and open state cavity barriers must comply with BS 476-20, EN 1366-4 and Association For Specialist Fire Protection (ASFP) technical guidance document 19.
When considering reduced gaps at fire barriers, the minimum gaps for different joint types are as follows: 12.5mm for sealed and closed joints, 19mm for labyrinth and baffled joints, and 25mm for open joints.
Various fire tests are conducted based on the scale and application. Small-scale tests for linear joint seals and open state cavity barriers must comply with BS 476-20, EN 1366-4, and ASFP technical guidance document 19. Medium-scale testing for perimeter barrier firestops and protected spandrel systems follows EN 1364. Large-scale system tests for cladding assemblies are carried out according to BS 8414-1/2, and the tested system is classified to BR 135.
More Information can be found on Fire Testing on some of the below links:
Nullifire Quelfire Hilti Video
Testing for rainscreen cavity barriers
In the late 1990s, Siderise began testing cavity barriers specifically for rainscreens, as prior to that, only assessments were available. The ad hoc B 476-20 barrier tests involved fixing the barrier in a cavity between fire-resisting walls.
During testing, the cavity barrier is installed to maintain a 25mm or 50mm gap, following the standard time/temperature curve at standard pressure. As the temperature increases, the intumescent material reacts by expanding. The key criteria for performance are the activation time and the ability of the intumescent to quickly close the cavity. It is important to note that not all intumescent materials behave the same way, as their reaction may vary at different temperatures and pressures.
For standard proprietary intumescent materials, there can be a significant time delay before they expand sufficiently to form a seal as the temperature rises. The activation time and expansion properties are critical factors for the seal’s performance, and a faster closure time is desired for better effectiveness.
Testing for ‘open state’ cavity barriers
Competing products can vary in performance, and not all may be suitable for their intended purpose. In 2014, the Association For Specialist Fire Protection (ASFP) addressed the need for classifying product performance by publishing a technical guidance document specifically for testing “open state” cavity barriers.
This document introduced a formal definition for open state cavity barriers, which are designed to provide ventilation and drainage in normal conditions but close or possess inherent fire-resistance properties in the event of a fire, ensuring fire separation within the cavity.
The ASFP technical guidance document established a standard performance requirement for effective closure. It states that the time taken for the cavity barrier to close must be measured and recorded. A successful cavity barrier must close within five minutes from the beginning of the test; otherwise, it is considered a failure. This standardized performance requirement ensures the reliability and effectiveness of cavity barriers during fire incidents.
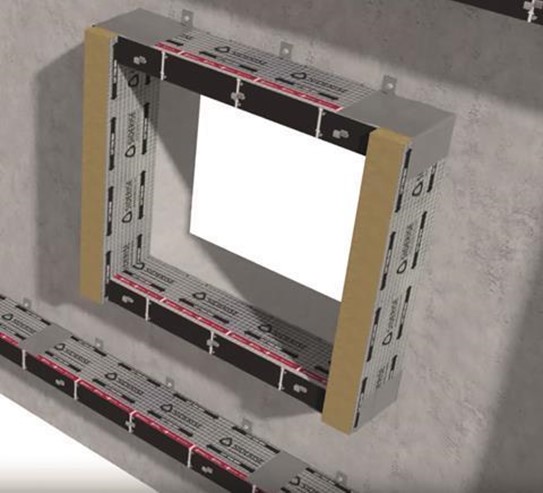
The performance of the seal is highly dependent on the activation time and expansion properties, with the “time to closure” being of utmost importance. Some companies have sought a faster closure limit, believing it achievable under test conditions.
Addressing closure time, the ASFP technical guidance document provides details on test configurations and failure criteria. It builds upon the existing linear joint seal test but incorporates modifications, such as the inclusion of upstands, to better simulate cavity construction. These refinements ensure that the testing accurately reflects the performance of cavity barriers in real-world scenarios.